Allow Me To Retort: Waterjet vs. Router
I seem to meet a lot of engineers. I don’t know why, but I meet a lot of them in the context of the ADV1. It might be that an inordinate number of engineers ride motorcycles. Maybe engineers like attending organized events that involve motorcycles: rallies, club meetings, etc. But, whatever group of riders I talk with, it seems a strange number of them are engineers. And mechanical engineers at that.
And they all have the same thing on their mind—they want to let me know that Pasq is doing it wrong.
We at Pasq have experimented and designed multiple ways to make a single-wheel motorcycle trailer. We first thought the best way to do this was to make the frame from welded aluminum tubing. But after some expensive trial and error, we found that we could make a stronger, lighter, more repairable trailer by cutting the frame out from ⅜” 6061-T6 aluminum plate, and then bolting everything together.
Here’s what they look like, fresh off the CNC router:
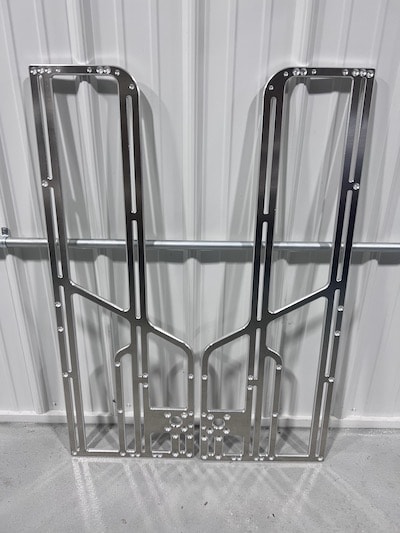
The keyword above is “cutting.” With our engineers and machinists, we have determined that the best way to cut our frames out is with a CNC router. It’s like that wood router you might have in your garage, but on steroids. It’s controlled by computers and is amazingly precise: a standard tolerance for a CNC machining service is typically ± 0.005” (0.13 mm).
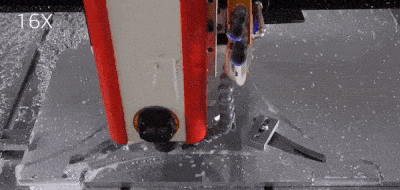
So, back to my engineer problem—the word “router” seems to set them off. Their eyes flick up and to the right as they recall bits and bobs of Professor Kumar’s lectures from back in the day. They then fix me with a death stare and proclaim in a loud and confident voice, “You are doing it wrong!”
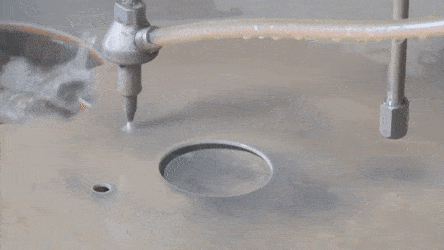
The implication is, “You’re not an engineer, but I—mechanical engineer extraordinaire—am here to save you!” I’m sure you, dear reader, believe I am surely exaggerating. How could mild mannered mechanical engineers be so bold as to tell you, “you’re doing it wrong!” I have had this conversation at least six times.
Reasons Engineers Give on We Should Use Water Cutters
- It’s faster.
- It’s cheaper.
- Bits for CNC routers wear out quickly and are expensive.
- It’s so much cooler technology!
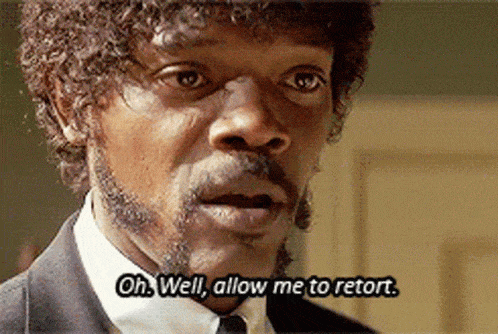
Reasons Why Pasq CNC Routers Their Frames
Rough vs. Smooth
Water cutters don’t just use water; the cutting stream includes fine particles that actually do much of the cutting. Those gritty particles impregnate the cut edge. The end result is rough finish on the cut edge of thick (⅜”) aluminum plate. We don’t want that…we want a smooth finish. If we use a water cutter, there would have to be a sanding or finishing step, which is slow and expensive.
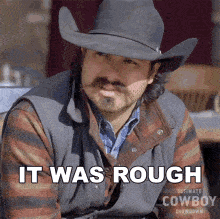
Chamfering
We are chamfering all the edges of the ADV1 to give it the look and feel we want—a more refined look. We would want to do this even if we water cut the frame pieces, but it takes less time if we just have the same machine cut and then chamfer the frame pieces.
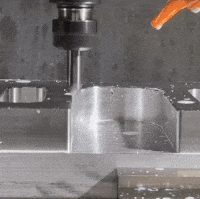
CNC Bits Are Not Fragile
We use the tried and true high speed steel cutters that work amazingly well! And our machinists do not understand the constant comments about them being really expensive and don’t last long. Our experience is cutter life is incredible on 6061-T6 aluminum. They do get dull, but not as quickly as some seem to think. Their cost does not have a significant impact on the cost of our trailers.
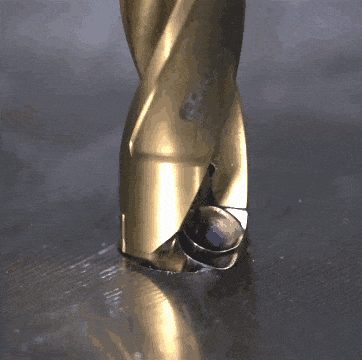
All Together
When you take all of these points together, using a CNC router to cut the frame of our trailers saves time on cleaning edges and having to use two separate processes on two separate machines: cutting and chamfering. By cutting and chamfering on the same machine, we don’t have to move the frame piece and then accurately reset it on a second machine. That makes up for some or all of the longer time it takes for the router to cut a piece versus a water cutter. The other main concern of the engineers is they seemed very worried we’d have to use dozens and dozens of router bits to get a few frames, which would be expensive. In our experience, that’s just not true.
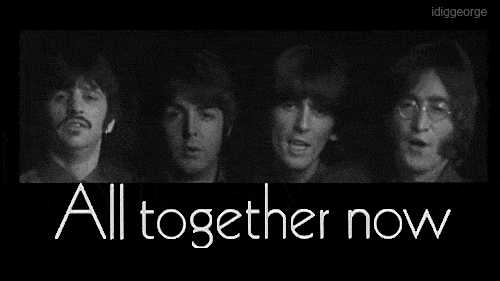
So, if you ended up on this page because one of the Pasq team handed you a card that said, “Allow me to retort,” hopefully you now understand the rationale behind our decision to go with CNC router cutting. And if you ended up here simply because it sounded interesting, thanks for reading all of this!
Oh, I forgot, the engineers are right…water cutting is pretty cool, but I’m partial to the fluid motions of a CNC router.